Into the Deep Robot Challenge
Our 2024-2025 Robot
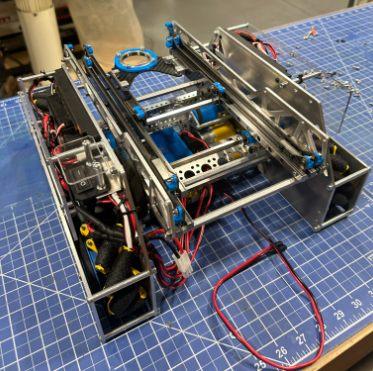
Our Main Robot Parts
We have 4 main robot elements, that are vital to the entire production!
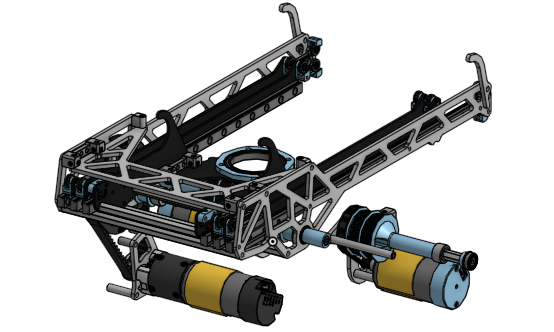
Hanging Mechanism
Custom-made transmission system drives the ascent mechanism using the drive motors. The mechanism shifts over a gear attached to the drive motor and generates enough torque to lift the robot up. Designed to achieve all three ascent levels and maintains a compact design.
Elevator Subsystem
Differential drive system helps control the vertical and rotational aspects of the lift’s motion. Driven by two motors placed on the bottom of the bot, the mechanism keeps the center of mass low.
A central axle’s rotation changes the angle of the lift in relation to the robot, enabling vertical and horizontal extension. The slides from the lift double as the ascent mechanism as well.
The differential drive offers easy control of rotational and vertical motion of the arm. An additional differential mechanism on the intake produces 6 degrees of freedom in the claw
Carbon fiber plates increase stiffness and minimize weight for precise elevator control.

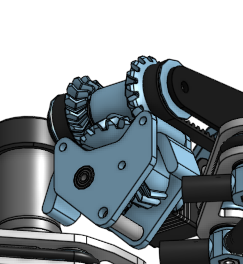
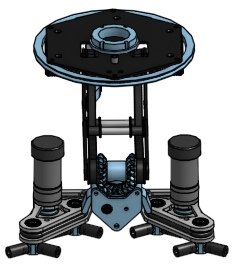
Intake Subsystem
Triangular contour of the claw is designed to fit perfectly into the surface of a sample. O-ring sweepers bring the desired sample flush to the plate of the robot, minimizing errors in pick up
Six degrees of freedom in total for the arm to pick up samples in any random orientation, with a second differential drive.
State machine and a second software FOV minimizes drivers’ effort. The geometry of the claw allows for pickup from any side of samples creating a pickup that is not clunky and doesn’t interfere with other robots
The claw’s geometry ensures a perfect fit, creating tight and efficient pickups that minimize errors.
Drivetrain
Compact chassis design using belt-driven mecannum wheels helps us design a compact yet functional robot
Low position of the drive motors lowers the robot’s center of gravity, increasing stability
Integration of optical odometry enables precise navigation in autonomous.
Integration of FOV software orients the robot to the driver’s frame of reference, simplifying driving
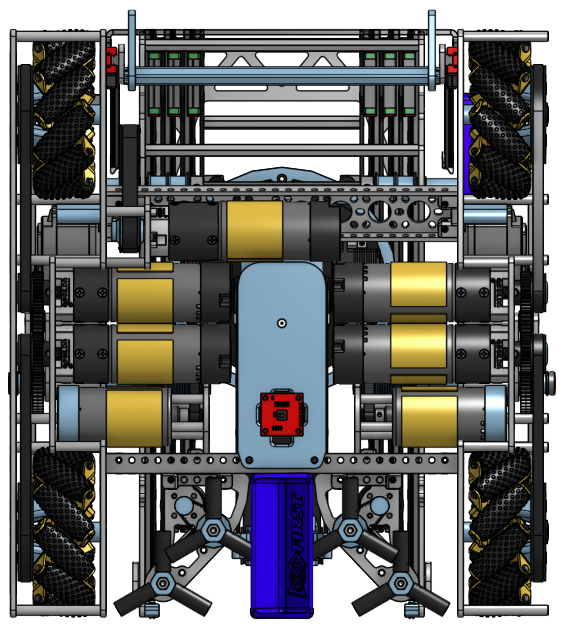
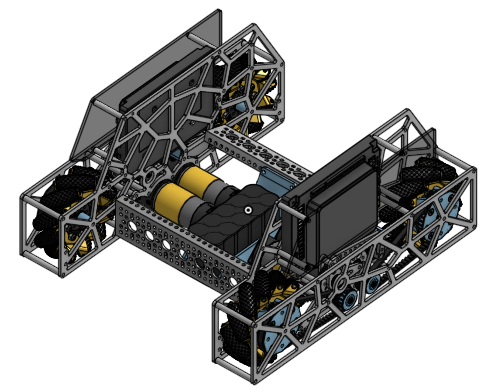
Software Design Process

The Big Ideas of our Software Process
Disciplined subsystem & Design History File based development process.
Driver centric FOV (in the drivetrain and intake) control that leveraged trigonometry.
Optical odometry using Roadrunner with autocorrection.
4 button sophisticated state machine design for simple driver control.
Complex PID + Motion Profiling for Differential control.